So today a regular client sent me a picture of a distressed downspout on her house.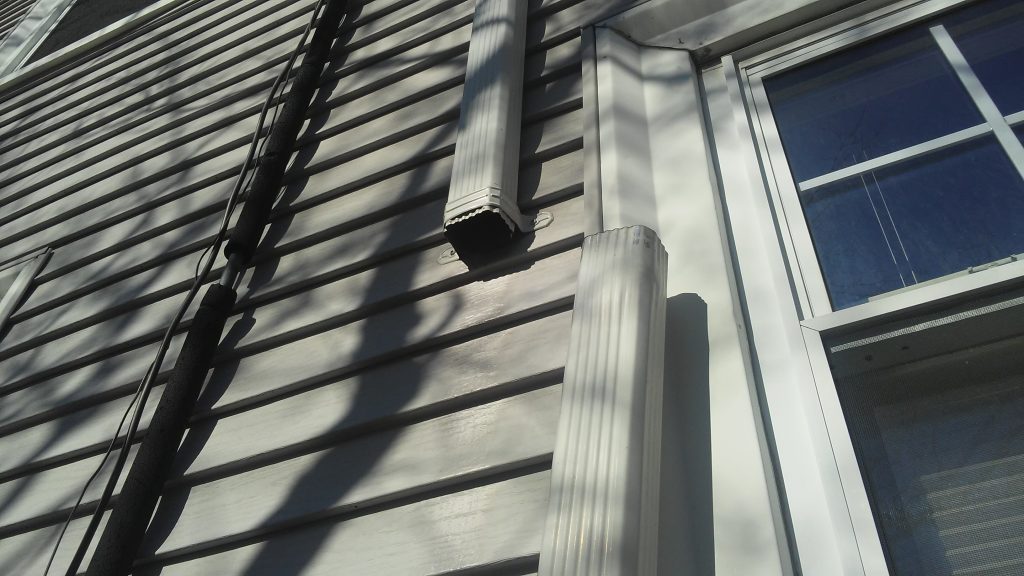
I looked at it and said, “oh this is going to be so easy, two screws and done.” silly me.
It’s a sad fact of my existence as a handyman, that well over 60% of the work I do is correcting improper installations. And oh boy was this an improper installation.
I didn’t really have time to take a lot of interim pictures as I was up on a ladder doing all this. Hopefully I can explain it verbally:
Standard four-inch metal downspouts are designed with one end crimped in a little bit so it can go into the end of the next piece. There’s no hard and fast rule, but the general sense is that you would have something like a 2 inch overlap. Another unwritten rule is that you have at least two points of attachment (to the house) for each section of pipe.
So as I looked closer at this problem child pipe, it became obvious that whoever had installed it originally, had only allowed for may be half an inch of overlap. And the only point of attachment for the entire pipe was down at the base of it.
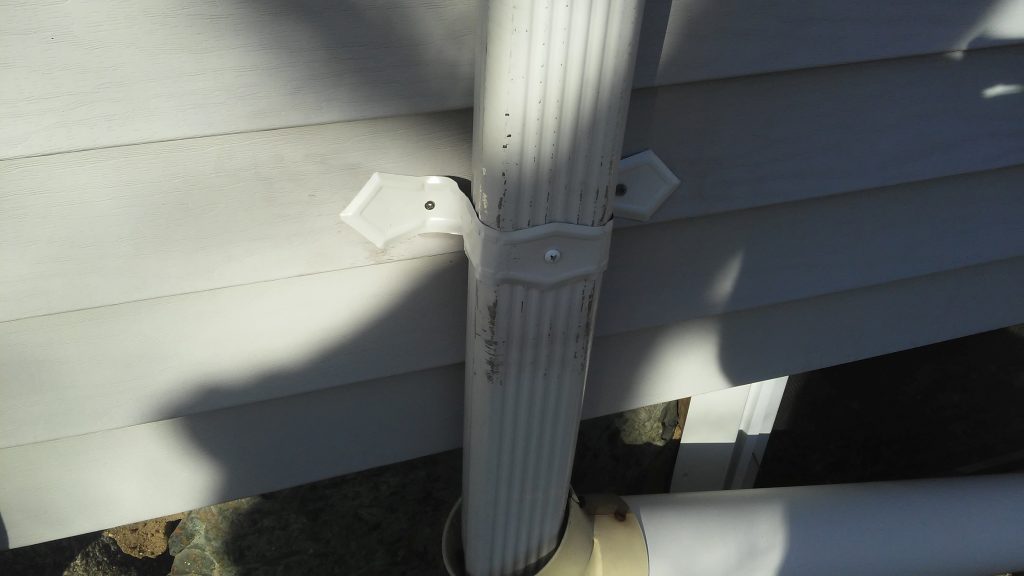
(Pic is of my fixed version with a screw anchoring pipe to the fastener.) And to add insult to injury, instead of just being a pipe emptying out, this pipe was screwed (with a rusting not stainless steel screw by the way) into a sizable drainpipe that was unsupported and constantly pulling the entire assembly down and and down and down. Gravity does that, and so over time, gravity had gradually pulled the pipe out of its unscrewed and just barely deep enough overlap connection with the pipe above, causing the total disconnect.
Because of the connection to the drainpipe below, it wasn’t really practical to raise the pipe up to get a one or 2 inch overlap between the two pipes. So, off to Home Depot, where I got a short section of pipe, cut it to about a 6 inch length, and essentially used it as a coupler between the top and bottom long pipes.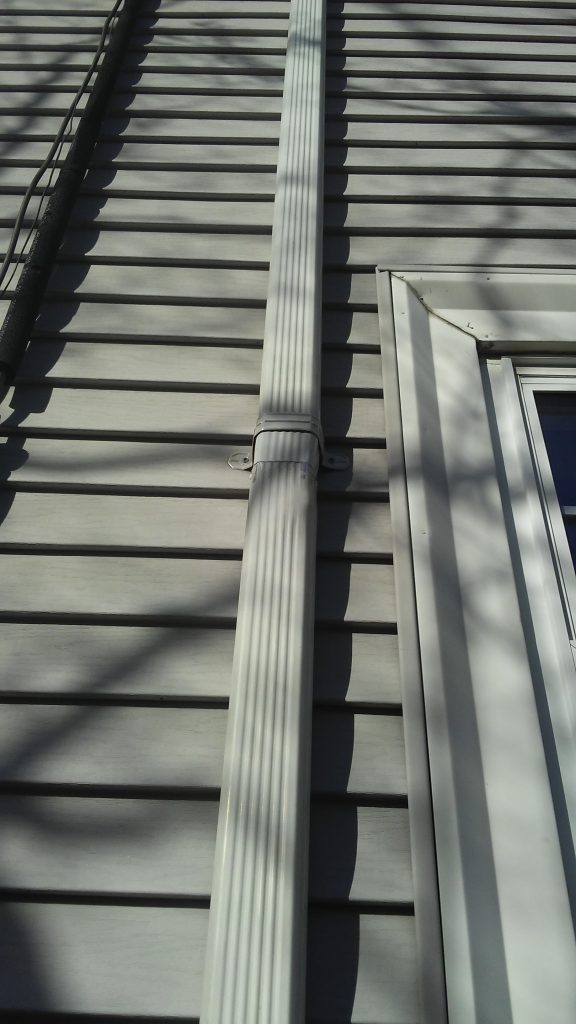
You can’t really see it because the attachment hardware covers up the top of the coupling joint, but unlike my predecessors, I used several stainless steel screws to attach the coupler to both the upper and lower pipe. Then I replaced the lower attachment hardware because it had become all bent and deformed. Between the new attachment hardware below, and the multiple screws above, it feels hard as a rock.
After I finished that job, I figured, if they did a cheap inadequate install here, they probably did another cheap inadequate install everywhere else. Sure enough, the exact same issue was just waiting to happen on another downspout at the front of the house. I installed an added fastener and put a screw through the fastener making sure that the pipe could not slip down any further. It was within an eighth of an inch of popping out of joint just like the other one. 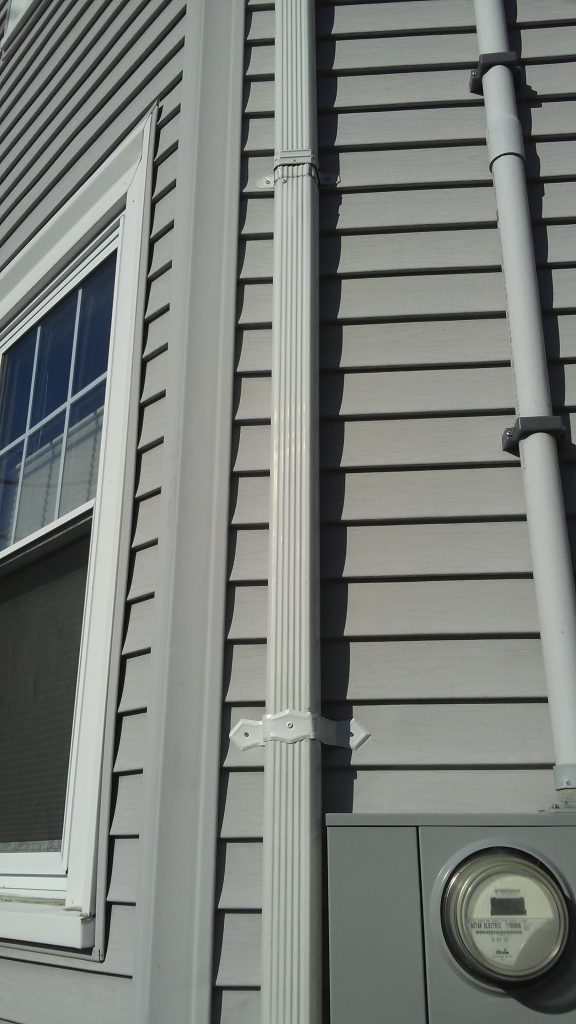
Downspouts are one of those areas of houses that, well, I don’t think there’s such a thing as a licensed downspout guy. Just about anybody can say they know how to put them in, and since it’s unpressurized water that’s outside, possible problems from bad installations take a long time to manifest. You only realize that the installation is wrong when you have a major monsoon rain and the water is not being directed away from the foundation properly. Or there’s some kind of leak somewhere and you don’t realize it til you get mold and termites.
Downspout installation does not get anywhere near the respect and attention it deserves. Caveat Emptor!